Nr.: 21/11 Hanau, 24. Oktober 2011
Hanau / Frankfurt – Die VACUUMSCHMELZE GmbH & Co. KG (Hanau) hat
ihren Klebe- und Korrosionsschutzlack VACCOAT® 20011 weiterentwickelt
und bietet ab sofort den Nachfolger VACCOAT® 30033 an: Der grün gefärbte
neue Einbrennlack sorgt für eine höhere Widerstandsfähigkeit bei den
Dauermagneten der VAC auf Basis von Selten-Erd-Legierungen, ganz besonders
unter extremen Bedingungen. Die Schutzschicht ist bis etwa 200°C
im Dauerbetrieb einsetzbar und übersteht Temperaturspitzen bis zu 250°C
über mehrere Stunden. Darüber hinaus bietet der neue Sprühlack eine höhere
Korrosionsbeständigkeit als der Vorgänger. Dank dieser Eigenschaften
eignet sich VACCOAT 30033 ganz besonders für Salzwasserumgebungen
oder für den Einsatz im Motorraum.
Beim Vorgänger, VACCOAT 20011, handelt es sich um einen hochfesten Klebeund
Korrosionsschutzlack. Allerdings waren, um diese beiden Eigenschaften in
einem Produkt zu vereinen, Kompromisse notwendig. Durch geschickte Umformulierung
der Basisrezeptur in Verbindung mit speziellen Zusatzstoffen, die die
Grundmaterialkorrosion verhindern, entstand nun mit VACCOAT 30033 ein ganz
neues Produkt. Gegenüber VACCOAT 20011 weist der neue Lack auf Epoxidharzbasis
eine etwa zwei- bis dreifache Standzeit in den relevanten Korrosionstests
auf – und ist damit also noch widerstandfähiger.
Mit VACCOAT 30033 werden auf Neodym-Eisen-Bor-Magneten bei einer üblichen
Schichtdicke von etwa 20?m problemlos Standzeiten von mehr als tausend
Stunden in den typischen beschleunigenden Korrosionstests für Dauermagnete
erzielt. Durch die hohe Beständigkeit beispielsweise in Salzwasserumgebungen
eignet sich VACCOAT 30033 ideal, um Magnete in Off-Shore-Windanlagen und
Gezeitenkraftwerken wirksam und nachhaltig vor Korrosion zu schützen. Ein anderer
Anwendungsfall ergibt sich im Auto: Hier lässt sich mit dem Einsatz von
VACCOAT 30033 ebenfalls die Lebensdauer der dort verwendeten Magnete ver-
längern. Häufig wird gerade in diesem Umfeld eine Kombination aus Standfestigkeit
im Salzsprühtest (nach DIN EN ISO 9227) bei gleichzeitiger Feuchtebeständigkeit
der Beschichtung benötigt.
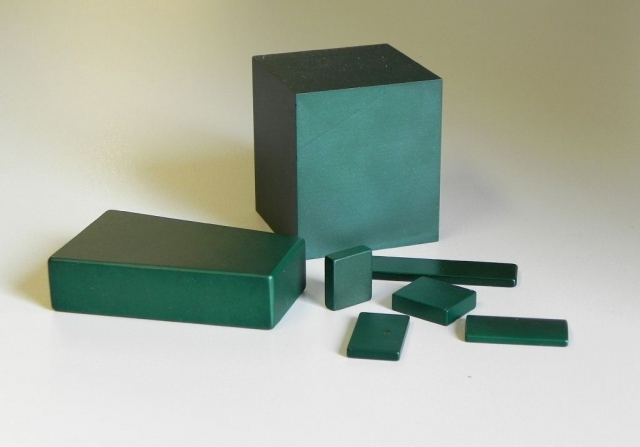